Team of young Blue Hens ride leading edge of jet technology
Consider the humble coffee cup. Its simple duties conceal a deceptively formidable character: The ceramic it is made of is harder than steel, and the scalding liquids it holds never seem to do it much harm.
Now imagine a roaring, flaming jet engine — possibly the pinnacle of 20th century power plant engineering — and try to envision what a touch of ceramics might do to make it even better.
A young and blade-sharp group of University of Delaware engineering graduates are doing just that at the Newark-based outpost of GE Aviation, which has been working for years to incorporate ceramic parts into the next generation of massive jetliner power plants. Through countless calculations, ceaseless tests and constant refinement, the four Blue Hens are pushing the final phase of GE’s quest to completion — not too many years after they won their UD mechanical engineering degrees.
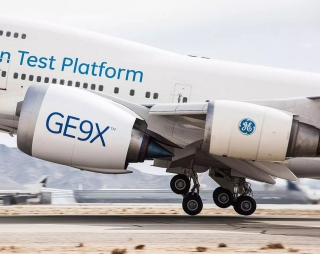
The GE9X engine (left) is much larger than engines that it is designed to replace. The GE9X is designed to be more powerful and more fuel efficient than previous engines. It scheduled to be used on the newest version of Boeing’s 777X, which has two engines and will be used for long-haul flights.
There’s Reid Bremble, Class of 2015, the plant’s guru of transforming raw materials into ceramic-based composite materials, and Vince Uathavikul, Class of 2007, a former furniture designer who came to GE seeking bold challenges. Tyler Walker, Class of 2013, left a good job with Chrysler to be here, and Sam Kurkoski, Class of 2014, already finds himself flying around the country fine-tuning production processes.
Meeting these men, it’s tempting for an older outsider to wonder at how they could be pushing technological boundaries at such an age. One is a mere 24, the others are not too far past that. Yet they speak with a maturity and commitment beyond their years; possess a steady-handed confidence forged in these high-temperature, high-pressure labs.
They know what they are working on is revolutionary. And it amazes them every day that they are the ones working on it.
“We’re doing something that is done nowhere else in the world,” said Walker, lead manufacturing engineer.
At its simplest level, their work seems simultaneously improbable and brilliant: Take sand and carbon (silicon carbide), bake it in an oven, stretch it out into fibers, then cover the fibers with more melted silicon carbide. The hardened result is a ceramic material, very distantly related to your morning coffee mug.
This ceramic — known as Ceramic Matrix Composite, or CMC — is the pit bull of materials technology. It’s light, strong, and can resist ferocious conditions. Use it on space ships, and not even the blazing heat of re-entry can penetrate it. Put parts made from it in a jet engine, and that engine will weigh less, and be able to run hotter and more efficiently.
First, though, someone has to figure out how to make the parts out of endless paper-thin sheets of CMC material, which has to be layered into molds like a super-high-tech lasagna. Then, they need to fine-tune the process so that it’s cost effective for GE to make the parts in large numbers and market them.
That’s where the UD crew comes in.
Already, the Newark team has invented production processes and made the earliest prototype parts for GE’s first-generation CMC-fortified engine, and now they’re busy fine-tuning the parts for its next big release — the GE9X engine being designed for the planned Boeing 777X jetliner.
GE has made a $1.5 billion bet that they will get it right — more than 700 of the giant 11-foot-diameter GE9X engines are already on order, and GE expects the market to grow tenfold over the next decade.
At the Newark plant, the main focus now is on three crucial GE9X parts: the liner of the combustion chamber where fuel is ignited; the nozzles that direct the flow of hot gasses; and the shroud that lines the hottest part of the engine.
Bremble oversees a very early part of that parts production: Fine-tuning the best ways to add a secret coating to the fibers and turn them into sheets.
“Without Reid, there’s no fiber, and without fiber, there are no parts,” said Austin Capone, CMC manufacturing engineering manager at the plant.
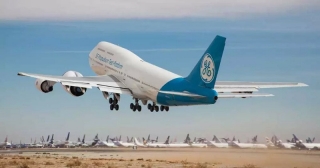
GE Aviation uses a Boeing 747 for what it calls its GE Propulsion Test Platform, with this test flight occurring in Victorville, California.
Walker then works to figure out ways to “lay up” the sheets into handmade, part-shaped molds so they can be baked.
“It’s an art,” said Walker, who must design the multi-piece metal molds from scratch. “A lot of times, it’s inventing the process. For a lot of the technology, there’s no recipe — the recipes are developed here.”
Meanwhile, Kurkoski leads the development of the nozzles.
“Having everyone under one roof as you’re developing is crucial,” Kurkoski said. “And I get to see these things from cradle to shipment.”
As a lead manufacturing engineer, Uathavikul is busy exploring ways to move beyond those stationary parts and put CMCs into rapidly moving components such as the turbine blades. But before that can happen, the priority is on constantly improving the manufacturing process for the GE9X, which flew for the first time in March and needs to be ready for certification next year. The 777X is expected to enter service in 2020.
When it does fly, the Blue Hens will be with it in spirit.
“I really did fall in love with UD,” said Kurkoski. “It really clicked for me, and I had a lot of hands-on experiences while I was here. I was well-prepared.”
The University of Delaware Magazine has other photographs of UD grads working for GE Aviation.